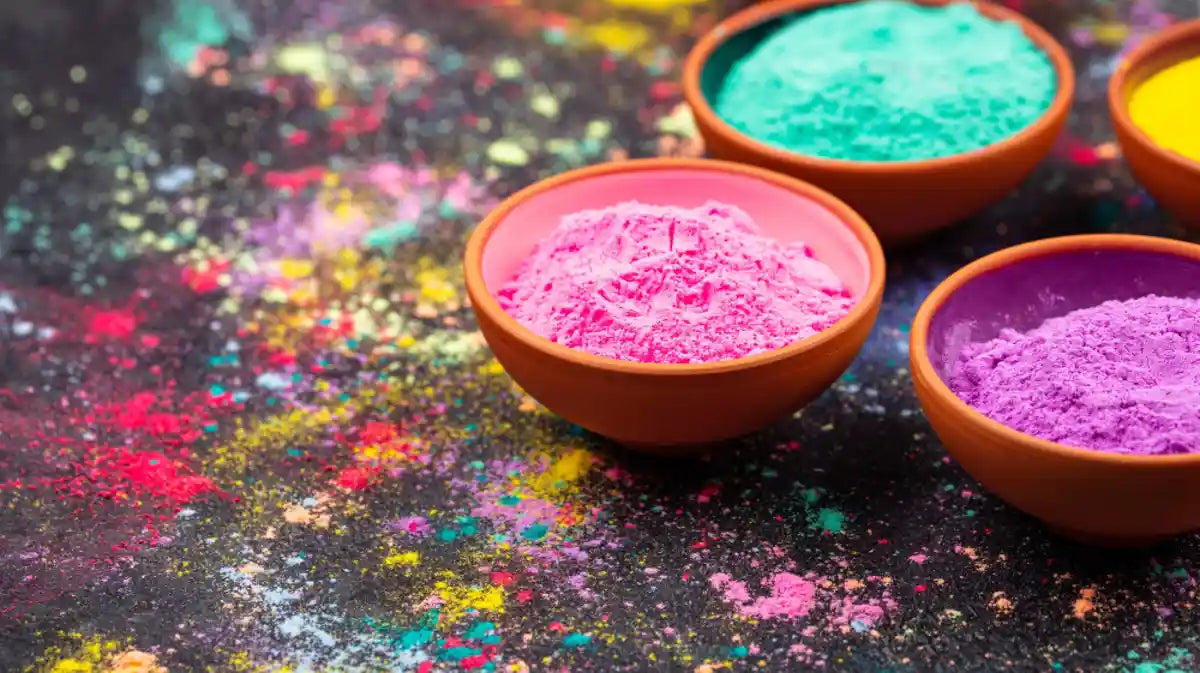
What is Electrostatic Powder Coating?
Powder coating is a completely dry coating system. It consists of electrically charged ground resin, pigment and other raw material particles and is sprayed onto the objects to be painted.
The materials to be painted are grounded, allowing the charged particles to adhere to the material before melting and sticking to each other in the curing ovens to create a smooth, durable and high-quality coating. Powder paints are divided into two categories: thermoset (heat cured) and thermoplastic. Heat cured powder paints are the most commonly used powder paints. They undergo an irreversible chemical change during the curing process and do not melt back into liquid form when heated again. Thermoplastic powder paints can be melted repeatedly by heating and solidify when cooled. They are especially suitable for applications with high film thicknesses where the most demanding performance requirements are required.
WHAT IS ELECTROSTATIC POWDER COATING?
Electrostatic powder painting is a solvent-free surface coating method. The coating material is very fine powder paint particles that form the final paint layer.
Powder paint is applied in the paint booth using special paint guns. Electrostatically charged powder paint particles adhere to the material to be painted in the booth as they pass through the gun and the coating process is completed. In order for the powder paint to adhere completely to the surface of the material, the material must also be grounded very well. Excessive paint is collected and put back into use thanks to the paint recovery system in the booth. The paint recovery system is one of the greatest economic advantages of electrostatic powder painting technology. After the material is coated with powder paint, it enters the baking oven. The oven temperature of 200ºC ensures that the powder paint melts and adheres to the material. As a result, a very durable, economical, environmentally friendly, wide-ranging and shiny surface coating is obtained.
Being solvent-free, surface quality, durability, paint recovery system, economy and environmental sensitivity make electrostatic powder coating a more attractive alternative to traditional painting processes.
Application of Powder Coating
Powder coating application consists of three main steps.
- Cleaning and pretreatment
- Powder coating application
- Baking
Cleaning and pretreatment
In order to get perfect results from the painting process, the part to be painted must be cleaned and pre-treated. There are various methods used in cleaning the part. Acidic cleaners give good results for inorganic dirt, while alkaline cleaners are more suitable for organic dirt. For other organic dirt, degreasing chemicals are used.
After this cleaning process, phosphating is usually required. However, for aluminum profiles used for architectural applications, passing them through a chromic acid solution gives better results.
Paint Application
Powder coating application is carried out by means of an electrostatic gun. There are two types of guns for this purpose, corona and tribo. In the corona type gun, the powder is electrostatically negatively charged as it leaves the gun thanks to a high voltage electrode located at the tip of the gun. Since the part to be painted is grounded, the electrostatically charged paint easily adheres to the part. However, sometimes the Faraday effect occurs in very recessed and protruding parts and the entry of the powder into the hollow areas can be problematic. In these cases, tribo type guns are used. In this type of gun, the paint is charged positively only by friction, without applying high voltage.
Baking
The powder coated part is placed in the oven. At this stage, the part is exposed to the time and temperature given in the paint's specifications. At this temperature, the paint first melts and forms a flat surface, then cures. At the end of this period, the painting process is completed after the part is removed from the oven. Powder Coating products generally cure in 10 minutes at 200 degrees. However, the 10-minute period mentioned here is started after the part reaches 200 degrees.
Process Efficiency of Powder Coating Technique
- The material usage efficiency in powder coating is approaching 100%. The excess sprayed powder coating particles are recycled and returned to the painting system for reuse. As a result, 1/2 to 1/3 less material is required in powder coating compared to wet paint.
- Powder Coating Automation Made Easy
- Three important factors that powder coating has provide solutions suitable for automatic application:
- - Electrostatic method; creates a wrapping effect and the powder is coated homogeneously on the product.
- -Easy to reach corners and recesses with powder coating.
- -Powder paint does not drip, making it easy to position the gun.
The Superiority of Powder Coating
The "Thixotropic" properties of the powder coating film ensure that the coating is equal to that obtained with a dry paint film. During the firing process, polymerization of the powder coating occurs, allowing the paint film to spread and harden on the product. As a result, significant improvements have been achieved in the coating obtained in terms of excellent resistance to abrasion, rust, chemical attack and generally harmful external factors, as well as facilitating application.
Environmental Protection
Electrostatic powder painting is a method that does not harm the environment; there are no volatile organic substances in the powder paint. This means that not only the environment is protected, but also the manufacturer has potential savings in terms of waste problems, chimney and duct cleaning, storage and worker health when compared to equivalent solvent-based painting systems.
Business Economics
- Electrostatic powder coating systems provide significant operating economy.
- Oversprayed powder paint is recycled and reused.
- There is no need for primer painting.
- They are used as received from the powder paint manufacturer and do not require mixing with solvent or similar processes before use.
- Filtered or desiccant air is sufficient.
Advantages of electrostatic powder paint
Electrostatic powder paint; long life in materials, economy, perfect surface coating, easy cleaning, environmentally friendly, It provides products that are easy to maintain, aesthetically pleasing and easy to use, with a wide variety of color options.
Where is Powder Coating Used?
- Aluminum industry
- Steel Door Industry
- Machinery Industry
- Lighting industry
- White goods industry
- Automotive Sub-Industry
- Metal Furniture Industry
- Steel Shelving Industry
- Park garden furniture and fence manufacturing
- Children's playgrounds manufacturing
- Manufacturing of agricultural tools and equipment
- Manufacturing of electrical panels
- Panel radiator manufacturing
- Bicycle manufacturing